Safety Incident Topic : Thermal Burns To Operator
Location Of Incident : Toledo Refinery, United States
Date Of Incident : 25 May, 2006
Brief Account Of Incident
A Vacuum Truck Operator at Toledo Refinery received significant second degree burns while preparing to offload hot water to a sump. The employee was transported by Life Flight to a hospital for treatment.The investigation team was not able to interview the injured employee. OSHA opened a formal investigation related to the incident that remains on-going at the time of this report.
Investigation
Onyx Industrial Services provides routine vacuum truck and pressure washing services to the refinery. The vacuum tank is fitted with an intake (vacuum valve) and discharge valve. Valves are four-inch, 1/4 turn ball valves with four inch camlock tailpieces. The operator was using a three inch hose for vacuuming (filling the tank) and another three-inch hose at the discharge sump. The intake valve on this truck fitted with a four-to-three inch reducer on the tail-piece to allow connection of a three-inch hose with camlock coupling.
After the incident, BP and Onyx inspected the vacuum truck. The vacuum truck was approximately ¾ full and the discharge valve was not leaking. The first person to arrive on-scene after the incident observed the discharge valve wide open, and a four-inch dust cap on the ground. The vacuum valve was closed, with the reducer, and dust cap installed. Manufacturer literature advises dust caps are not intended to contain hazardous materials or pressure.The injured had completed a Job Safety Analysis the day of the incident. He was wearing fire retardant clothing, safety glasses, hard hat, work boots and gloves.
What Went Wrong (Critical factors)
The injured either failed to notice the discharge valve was open during inspection, or opened the discharge valve before removing the four inch dust cap. The employee was positioned immediately behind the truck. As he removed the four-inch dust cap, he was exposed to the released contents of the vacuum truck.
Critical factors:
CF1: the technician removed cap from the discharge tailpiece of the vacuum truck while the discharge valve was in an open position
CF2: an inadequately protected technician burned from contact with hot water (estimated at 150 degrees or greater)
Possible Immediate Causes
- Unintentional error, improperly prepared equipment·
- Inadequate protective equipmentPossible System Causes·
- Inappropriate course of action (steps to offload truck)· Identification of worksite hazard (hot fluid, dust cap use, PPE)·
- Identifation of critical safe behaviours·
- Method of verifying absence of hot water behind cap
Key Learnings (addressed by actions)
1· Do you positively verify absence of thermal hazards before removing caps, plugs or valves from fixed andmobile equipment?
2· What safeguards are in place to manage fluids at temperatures >120degree F? (second degree burns occurwith exposure to hot fluids in five seconds at 140 degress F and one second at temperatures of 158 degrees F)
3· Is your equipment and that of your contactors designed to minimize the consequences of human error?
4· What PPE is required when transferring hot fluids?
5· How do you verify that contractors are conforming to their written HSE Plans (e.g equipment inspection, training, procedures, assesment)?
24 June 2006
16 June 2006
Electrical Flash Over
Safety Incident Topic : Electrical Flash Over
Location Of Incident : Kuantan, Malaysia
Date Of Incident : 24th July, 2005
Brief Account Of Incident
A lost time injury incident occurred when a contractor worker was exposed to a severe electrical flash-over while servicing the 11KV cable connection bar in a substation during a turnaround.
Outcome
First degree burn due to severe electrical flash-over.
Active Failures
The Active Failure leading to the incident was the 11KV cable connection bar was still energized when the contractor worker applied the earth bonding clamps resulting in a severe electrical flash-over.
Lessons Learned
1. Two separate PTWs were issued for the same activity:
i) servicing of front and back portion of switchboard and
ii) switching for isolation of front portion of the switchboard. A single PTW shall be issued for one activity and the switching for isolation shall be recorded in the Electrical Isolation Certificate.
2. The following shortcomings were observed in permitting processi) PTW – electrical hazard not identified, inadequate precautions & electrical PPEs not specified and contractorworker did not signed andii) Electrical Isolation Certificate – Lock-out and tag-out section not filled, Competent Person signing is not qualifiedBO and inadequate briefing/communication between issuer and receiver. The established PTW procedure shall bestrictly enforced and audited regularly to ensure full compliance.
3. The practice of radio-called a competent person to ask for approval for permit/certificate and then signed by anotherparty shall be stopped.
4. Inadequate communication and coordination between different turnaround teams and contractors during execution of works could result in miscommunication and different understanding of an intent.
5. Established lock-out and tag-out procedure shall be strictly enforced including use of tag, dedicated locks and key box for control of issuance of locks & keys.
6. Correct method of applying earth bonding clamps shall be used.
7. If you are working on an electrical equipment, never assume it is de-energised unless tested and confirmed byyourself.
Location Of Incident : Kuantan, Malaysia
Date Of Incident : 24th July, 2005
Brief Account Of Incident
A lost time injury incident occurred when a contractor worker was exposed to a severe electrical flash-over while servicing the 11KV cable connection bar in a substation during a turnaround.
Outcome
First degree burn due to severe electrical flash-over.
Active Failures
The Active Failure leading to the incident was the 11KV cable connection bar was still energized when the contractor worker applied the earth bonding clamps resulting in a severe electrical flash-over.
Lessons Learned
1. Two separate PTWs were issued for the same activity:
i) servicing of front and back portion of switchboard and
ii) switching for isolation of front portion of the switchboard. A single PTW shall be issued for one activity and the switching for isolation shall be recorded in the Electrical Isolation Certificate.
2. The following shortcomings were observed in permitting processi) PTW – electrical hazard not identified, inadequate precautions & electrical PPEs not specified and contractorworker did not signed andii) Electrical Isolation Certificate – Lock-out and tag-out section not filled, Competent Person signing is not qualifiedBO and inadequate briefing/communication between issuer and receiver. The established PTW procedure shall bestrictly enforced and audited regularly to ensure full compliance.
3. The practice of radio-called a competent person to ask for approval for permit/certificate and then signed by anotherparty shall be stopped.
4. Inadequate communication and coordination between different turnaround teams and contractors during execution of works could result in miscommunication and different understanding of an intent.
5. Established lock-out and tag-out procedure shall be strictly enforced including use of tag, dedicated locks and key box for control of issuance of locks & keys.
6. Correct method of applying earth bonding clamps shall be used.
7. If you are working on an electrical equipment, never assume it is de-energised unless tested and confirmed byyourself.
15 June 2006
Cutting Work Incident
Safety Incident Topic : Cutting Work
Location Of Incident : Lingen, Germany
Date Of Incident : 19th August, 2005
Brief Account Of Incident
A worker from an outside contracting company (a repair company for steam boilers) was given the task of separating some steel pipes from a bundle of superheater pipes (1a) in Steam Boiler 2. To cut the pipes he used an angle grinder (P=2.2KW) with a cutting disk (D=230mm). When he was cutting out his third pipe, he put the angle grinder to the pipe at a height of about 1.8 m from the work platform. He switched the angle grinder to continuous operation mode. The pipe began to work loose whilst he was cutting through it and the cutting disk got stuck. The angle grinder recoiled and hit the workman on the left side of his chest. The angle grinder lodged in his work clothing. A colleague who was present prevented any further injury by switching the power off. The injured man was able to climb down from the scaffolding and leave the enclosed space unaided. The security guards called the ambulance men, who carried out first aid on him before taking him to the local hospital.The man was discharged after receiving treatment in the outpatients department, and the following day he was given lighter work to do (RWI).
Outcome
- Lacerations in the left chest area which responded to medical treatment in hospital (MTC).
- If the injury had been to his neck, the accident would have to have been classified as a major incident (MIA).
Possible Immediate Causes
- Unfavourable working position.
- The man was overtaxing his body at the time.
- Incorrect cutting sequence. (The first cut should have been in the lower section).
- The decision to start cutting at the top was the wrong one.
- It was a seemingly easy routing task and the man had not thought it through properly).
- Noise was a hazard. The pipe was under tension. The tools / working environment presented a mechanical hazard.
- The working position and ambient temperature were ergonomically unfavorable.
Possible Causes in the System
- Exhaustion as a result of the work load.
- Reduced performance as a result of the high room temperature.
- The man felt he had to finish the job quickly.
- The contracting company’s system for informing employees about work-related incidents is capable of improvement.
What Went Wrong
- The pipe which was to be cut out was under tension.
- In the position where it was, the angle grinder could not be operated safely.
- The angle grinder had been switched over to continuous mode.
What Went Well
- His colleague was on the spot to offer immediate help.
- The security guard had the workmen in view and was able to alarm the emergency services at the refinery immediately.
- The rescue team worked quickly and professionally.
Lessons learned
- It is important not to underestimate potential hazards from routine jobs.
Recommendations
- Select prudently when choosing which tools to work with.
- Angle grinders should not be switched to continuous mode when working in an unusual position.
- Before each separate stage in the work, the workmen must assess the possible dangers, independently of the ambient conditions, and should take the necessary preventive steps.
Location Of Incident : Lingen, Germany
Date Of Incident : 19th August, 2005
Brief Account Of Incident
A worker from an outside contracting company (a repair company for steam boilers) was given the task of separating some steel pipes from a bundle of superheater pipes (1a) in Steam Boiler 2. To cut the pipes he used an angle grinder (P=2.2KW) with a cutting disk (D=230mm). When he was cutting out his third pipe, he put the angle grinder to the pipe at a height of about 1.8 m from the work platform. He switched the angle grinder to continuous operation mode. The pipe began to work loose whilst he was cutting through it and the cutting disk got stuck. The angle grinder recoiled and hit the workman on the left side of his chest. The angle grinder lodged in his work clothing. A colleague who was present prevented any further injury by switching the power off. The injured man was able to climb down from the scaffolding and leave the enclosed space unaided. The security guards called the ambulance men, who carried out first aid on him before taking him to the local hospital.The man was discharged after receiving treatment in the outpatients department, and the following day he was given lighter work to do (RWI).
Outcome
- Lacerations in the left chest area which responded to medical treatment in hospital (MTC).
- If the injury had been to his neck, the accident would have to have been classified as a major incident (MIA).
Possible Immediate Causes
- Unfavourable working position.
- The man was overtaxing his body at the time.
- Incorrect cutting sequence. (The first cut should have been in the lower section).
- The decision to start cutting at the top was the wrong one.
- It was a seemingly easy routing task and the man had not thought it through properly).
- Noise was a hazard. The pipe was under tension. The tools / working environment presented a mechanical hazard.
- The working position and ambient temperature were ergonomically unfavorable.
Possible Causes in the System
- Exhaustion as a result of the work load.
- Reduced performance as a result of the high room temperature.
- The man felt he had to finish the job quickly.
- The contracting company’s system for informing employees about work-related incidents is capable of improvement.
What Went Wrong
- The pipe which was to be cut out was under tension.
- In the position where it was, the angle grinder could not be operated safely.
- The angle grinder had been switched over to continuous mode.
What Went Well
- His colleague was on the spot to offer immediate help.
- The security guard had the workmen in view and was able to alarm the emergency services at the refinery immediately.
- The rescue team worked quickly and professionally.
Lessons learned
- It is important not to underestimate potential hazards from routine jobs.
Recommendations
- Select prudently when choosing which tools to work with.
- Angle grinders should not be switched to continuous mode when working in an unusual position.
- Before each separate stage in the work, the workmen must assess the possible dangers, independently of the ambient conditions, and should take the necessary preventive steps.
Release Of Hydrocarbon
Safety Incident Topic : Release Of Hydrocarbon
Location Of Incident : Hull, UK
Date Of Incident : 20th April, 2006
Brief Account Of Incident
During the start-up of the dehydration section of the DF2 plant, approximately 30tes of DIPE (Di-isopropylether) and 53tes of Acetic Acid were released in to the plant’s open channel trade effluent system from the base of steam stripper C205. This release began when C205 was started up with valve ‘A’ in the open position. This valve is normally closed during start-up and normal operation of the unit as referenced in the local procedures. With this valve open, C205 was gradually over-loaded with hydrocarbons and experienced high operating pressures. To maintain the start-up and prevent C205 tripping on high-pressure, the control temperature was deliberately kept low, leading to the loss of hydrocarbons from C205 base to effluent. Short duration pressure spikes had been experienced during start-ups on C205 in the past and the duty shift team felt that the column would recover (as previously) if left operating in this manner. Limited plant reviews took place to determine the cause of this sustained poor control.
DIPE is used in this part of the process to break the Acetic Acid/water azeotrope. Normally, with valve ‘A’ closed, water (with residual hydrocarbons) flows from the base of liquid-liquid separator C213 to the E204 condensers before undergoing further separation in decanter D204. With valve ‘A’ open the system hydraulics allow back-flow of condensed hydrocarbons from the overheads of the Azeotrope column C204, directly in to C205. This was initially DIPE, but later became rich in Acetic Acid when the reflux back to C204 was lost.
High TOC levels were first recorded by a local effluent on-line analyser at 19:55hrs on the 20th April and were further confirmed by spot sample effluent results (that were being taken every four hours) and continued until the unit was shutdown and isolated at 08:09hrs on the 21st April. Effluent had already been diverted to on-site storage before this event, so operating teams were confident there would be no breaches of consent.
Potential Outcome
DIPE is a highly flammable immiscible hydrocarbon solvent with a low specific gravity, so readily floats on water. C205 base drops in to an open channel that passes through the plant before reaching the local effluent pit. With such a large quantity of highly flammable material in an open channel, there was the potential for combustion with resulting escalation.
What Went Wrong (Critical Factors)
· Engineering/Design. Valve ‘A’ should not have been open at start-up. The valve was not part of a locked closed valve register. Potential back-flow from E204 had not been recognised in any previous process safety studies.
· Inattention/Lack of Awareness. Failure to adequately respond to high TOC levels from both on-line analysis and spot sample results and failure to appreciate volumes of hydrocarbons involved. Limited plant investigation took place.
· Communication. Local Shift Site Manager (SSM) was not informed. Duty shift teams did not use local procedures for guidance on the actions to take on activation of high TOC alarm.
· Poor judgement. Mistrust of local TOC analyser. Persistent operation of C205 at low temperatures to avoid high pressure spikes/trips, believing column control would recover naturally.
What Went Well
· There were no breaches of consent, as effluent was already diverted to on-site storage as part of the plant re-start.
· The DIPE was recovered in the DF2 local effluent system and removed for off-site disposal.
Lessons Learned
· To immediately investigate and respond to any unexpected sustained rises in local effluent TOC results from on-line or spot sample analysis.
· To ensure process bypass valves are included in the plant’s locked valve register
· To improve communication between shift operating teams and the local SSM.
Key Messages
· To actively investigate any abnormal effluent condition and seek further support as necessary.
· Reinforce the expectation that operating teams shut the plant down rather than trying to recover from a persistent process upset condition.
Location Of Incident : Hull, UK
Date Of Incident : 20th April, 2006
Brief Account Of Incident
During the start-up of the dehydration section of the DF2 plant, approximately 30tes of DIPE (Di-isopropylether) and 53tes of Acetic Acid were released in to the plant’s open channel trade effluent system from the base of steam stripper C205. This release began when C205 was started up with valve ‘A’ in the open position. This valve is normally closed during start-up and normal operation of the unit as referenced in the local procedures. With this valve open, C205 was gradually over-loaded with hydrocarbons and experienced high operating pressures. To maintain the start-up and prevent C205 tripping on high-pressure, the control temperature was deliberately kept low, leading to the loss of hydrocarbons from C205 base to effluent. Short duration pressure spikes had been experienced during start-ups on C205 in the past and the duty shift team felt that the column would recover (as previously) if left operating in this manner. Limited plant reviews took place to determine the cause of this sustained poor control.
DIPE is used in this part of the process to break the Acetic Acid/water azeotrope. Normally, with valve ‘A’ closed, water (with residual hydrocarbons) flows from the base of liquid-liquid separator C213 to the E204 condensers before undergoing further separation in decanter D204. With valve ‘A’ open the system hydraulics allow back-flow of condensed hydrocarbons from the overheads of the Azeotrope column C204, directly in to C205. This was initially DIPE, but later became rich in Acetic Acid when the reflux back to C204 was lost.
High TOC levels were first recorded by a local effluent on-line analyser at 19:55hrs on the 20th April and were further confirmed by spot sample effluent results (that were being taken every four hours) and continued until the unit was shutdown and isolated at 08:09hrs on the 21st April. Effluent had already been diverted to on-site storage before this event, so operating teams were confident there would be no breaches of consent.
Potential Outcome
DIPE is a highly flammable immiscible hydrocarbon solvent with a low specific gravity, so readily floats on water. C205 base drops in to an open channel that passes through the plant before reaching the local effluent pit. With such a large quantity of highly flammable material in an open channel, there was the potential for combustion with resulting escalation.
What Went Wrong (Critical Factors)
· Engineering/Design. Valve ‘A’ should not have been open at start-up. The valve was not part of a locked closed valve register. Potential back-flow from E204 had not been recognised in any previous process safety studies.
· Inattention/Lack of Awareness. Failure to adequately respond to high TOC levels from both on-line analysis and spot sample results and failure to appreciate volumes of hydrocarbons involved. Limited plant investigation took place.
· Communication. Local Shift Site Manager (SSM) was not informed. Duty shift teams did not use local procedures for guidance on the actions to take on activation of high TOC alarm.
· Poor judgement. Mistrust of local TOC analyser. Persistent operation of C205 at low temperatures to avoid high pressure spikes/trips, believing column control would recover naturally.
What Went Well
· There were no breaches of consent, as effluent was already diverted to on-site storage as part of the plant re-start.
· The DIPE was recovered in the DF2 local effluent system and removed for off-site disposal.
Lessons Learned
· To immediately investigate and respond to any unexpected sustained rises in local effluent TOC results from on-line or spot sample analysis.
· To ensure process bypass valves are included in the plant’s locked valve register
· To improve communication between shift operating teams and the local SSM.
Key Messages
· To actively investigate any abnormal effluent condition and seek further support as necessary.
· Reinforce the expectation that operating teams shut the plant down rather than trying to recover from a persistent process upset condition.
14 June 2006
Forklift Incident
Safety Incident Topic : PTA Forklift Incident
Location Of Incident : Kuantan, Malaysia
Date Of Incident : Not Known
Brief Account Of Incident
After carrying out re-bagging of a damaged PTA bag (1.1 tone) using two forklift trucks, one of the forklift trucks driver got out of the cab to remove the empty bag, as he was standing in front of his forklift and leaning forward to remove the empty bag from the forks of the truck, the second forklift truck (which was now transporting the full bag) made contact with him as the truck driving forward and turning to get out of the gate. This contact knocked the person on to the stationary forklift. The Injured person was sent to local hospital by the emergency response team and given a comprehensive medical check. He was discharged later that morning, suffering only localized bruising.
Possible Immediate Cases
Improper use of equipment
The re-bagging operation should use the fixed hoist rather than using two Forklifts.
Improper decision-making or lack of judgment
The Injured Person stand at a very dangerous position but he did not pay much attention on it.
Routine activity without thought
The Forklift Driver just reverse the Forklift and drive forward, turn without noticing that the person is just in front of his Forklift.
Congestion or restricted motion
The Packaging area is too small and there is another Forklift parking there to limit the space for the Forklift movement
Location Of Incident : Kuantan, Malaysia
Date Of Incident : Not Known
Brief Account Of Incident
After carrying out re-bagging of a damaged PTA bag (1.1 tone) using two forklift trucks, one of the forklift trucks driver got out of the cab to remove the empty bag, as he was standing in front of his forklift and leaning forward to remove the empty bag from the forks of the truck, the second forklift truck (which was now transporting the full bag) made contact with him as the truck driving forward and turning to get out of the gate. This contact knocked the person on to the stationary forklift. The Injured person was sent to local hospital by the emergency response team and given a comprehensive medical check. He was discharged later that morning, suffering only localized bruising.
Possible Immediate Cases
Improper use of equipment
The re-bagging operation should use the fixed hoist rather than using two Forklifts.
Improper decision-making or lack of judgment
The Injured Person stand at a very dangerous position but he did not pay much attention on it.
Routine activity without thought
The Forklift Driver just reverse the Forklift and drive forward, turn without noticing that the person is just in front of his Forklift.
Congestion or restricted motion
The Packaging area is too small and there is another Forklift parking there to limit the space for the Forklift movement
13 June 2006
Falling Nearmiss
Safety Incident Topic: Screen From Shroud On Roof Ventilation Fan Falls
Location Of Incident: Canada
Date Of Incident: 21th June 2003
Brief Account Of Incident
While using the overhead crane to move a barrel of lube oil, the screen from a fan shroud on one of the roof ventilation fans became dislodged possibly by the passing crane and fell approximately 40 ft. to the compressor deck below. The screen, measuring approx. 5 ft in diameter and weighing 40 lbs (see Photo #1 below) missed the person operating the crane by a distance of 15 to 20 ft. Fortunately; he was the only person in the Compressor Building at the time.
What Went Wrong
A self-taping screw and tab holding the screen in place failed (possibly due to fatigue caused by vibration) allowing the screen to hang lower, and into the path of the overhead crane where it was caught and pulled loose.
What Went Well
- No injuries or property damage occurred as a result of this incident
- The fan was immediately locked out and tagged to prevent further use until inspected.
- An investigation was conducted and follow-up action promptly implemented.
System Root Causes
Inadequate technical design: The screens are held in place by only 4 small tabs welded to the screen material and secured to the fan shroud with self-taping screws. This design for securing the screens is evidently prone to failure, as other broken tabs and screws were also found on other fan screens.
Actions
- A Management of Change was initiated and the remaining screens have been temporarily removed.
- The manufacturer of the fan assembly has been made aware of problem and asked to design a better means of securing the fan screens to the shrouds. All screens will then be reinstalled
Location Of Incident: Canada
Date Of Incident: 21th June 2003
Brief Account Of Incident
While using the overhead crane to move a barrel of lube oil, the screen from a fan shroud on one of the roof ventilation fans became dislodged possibly by the passing crane and fell approximately 40 ft. to the compressor deck below. The screen, measuring approx. 5 ft in diameter and weighing 40 lbs (see Photo #1 below) missed the person operating the crane by a distance of 15 to 20 ft. Fortunately; he was the only person in the Compressor Building at the time.
What Went Wrong
A self-taping screw and tab holding the screen in place failed (possibly due to fatigue caused by vibration) allowing the screen to hang lower, and into the path of the overhead crane where it was caught and pulled loose.
What Went Well
- No injuries or property damage occurred as a result of this incident
- The fan was immediately locked out and tagged to prevent further use until inspected.
- An investigation was conducted and follow-up action promptly implemented.
System Root Causes
Inadequate technical design: The screens are held in place by only 4 small tabs welded to the screen material and secured to the fan shroud with self-taping screws. This design for securing the screens is evidently prone to failure, as other broken tabs and screws were also found on other fan screens.
Actions
- A Management of Change was initiated and the remaining screens have been temporarily removed.
- The manufacturer of the fan assembly has been made aware of problem and asked to design a better means of securing the fan screens to the shrouds. All screens will then be reinstalled
Workforce Fatality
Safety Incident Topic : Fatality As A result From Fall
Location Of Incident : Krasnogorsk Rayon, Russia
Date Of Incident : Not Known
Brief Account Of Incident
Leonid Novokovski a 46 year employee of General Contractor Acis was blown off a 5 m (approximately) high canopy roof during construction of a new Service Station. Tragically, he died as a result of the fall.
Leonid together with 2 fellow employees started to complete the roof by fixing the last row of sheet metal to a steel carcass. All 3 were wearing safety harnesses. Leonid removed his harness for reasons not yet known. A gust of wind blew the 4mx1m sheet and Leonid and his 2 co-workers off the roof. Leonid fell to the ground breaking his spinal chord in the region of his neck. His 2 co-workers, wearing safety harnesses, were uninjured. An ambulance was immediately summoned and arrived after 12 minutes. Leonid was pronounced dead by the ambulance doctor. The police arrived at 3 pm. Experienced contractor management was on site at the time of the accident as was a permanently stationed BP representative.
Acis informed the BP office of the incident at approximately 3 pm. An immediate attempt was made to contact the PUL and he was contacted within an hour. Within 3 hours the BUL, the GVP and R&M CEO’s Chief of staff had been briefed. An incident team was dispatched to the site and the contractor’s senior management was also summoned to the site. Work was halted on the site and another construction site. resumption of work will be preceded by a Safety Time Out.
Leonid’s twin brother and nephew were working on the site. (The nephew was on the roof with Leonid.) They are in a state of shock and every effort is being made to address their emotional needs. Leonid had worked with Acis since 9/8/03. He had received full safety training. He was Ukrainian from the town of Ordgenikidze in Dniepropetrovsk region.
An investigation team is being formed and working close with TNK/BP organization
Location Of Incident : Krasnogorsk Rayon, Russia
Date Of Incident : Not Known
Brief Account Of Incident
Leonid Novokovski a 46 year employee of General Contractor Acis was blown off a 5 m (approximately) high canopy roof during construction of a new Service Station. Tragically, he died as a result of the fall.
Leonid together with 2 fellow employees started to complete the roof by fixing the last row of sheet metal to a steel carcass. All 3 were wearing safety harnesses. Leonid removed his harness for reasons not yet known. A gust of wind blew the 4mx1m sheet and Leonid and his 2 co-workers off the roof. Leonid fell to the ground breaking his spinal chord in the region of his neck. His 2 co-workers, wearing safety harnesses, were uninjured. An ambulance was immediately summoned and arrived after 12 minutes. Leonid was pronounced dead by the ambulance doctor. The police arrived at 3 pm. Experienced contractor management was on site at the time of the accident as was a permanently stationed BP representative.
Acis informed the BP office of the incident at approximately 3 pm. An immediate attempt was made to contact the PUL and he was contacted within an hour. Within 3 hours the BUL, the GVP and R&M CEO’s Chief of staff had been briefed. An incident team was dispatched to the site and the contractor’s senior management was also summoned to the site. Work was halted on the site and another construction site. resumption of work will be preceded by a Safety Time Out.
Leonid’s twin brother and nephew were working on the site. (The nephew was on the roof with Leonid.) They are in a state of shock and every effort is being made to address their emotional needs. Leonid had worked with Acis since 9/8/03. He had received full safety training. He was Ukrainian from the town of Ordgenikidze in Dniepropetrovsk region.
An investigation team is being formed and working close with TNK/BP organization
12 June 2006
Toxic Vapor Released
Safety Incident Topic : Vent of styrene vapors
Location Of Incident : Wingles, france
Date Of Incident : 28th, April 2006
Brief Account Of Incident
the reactor was vented for 10 minutes while full cooling At 8h00 pm , April 28, 2005 , an operational problem due to too a high polymer melt viscosity led to a an emergency shut-down of crystal line n° 2 in Wingles site. As per the emergency procedure, rarely used, was applied . The estimated vapor release is 1.3 t . Under weak windy conditions, styrene odors were detected by neighborhood community. Fire brigade has been called for enquiry. The odor disappeared within 30 minutes and the operations were successfully and safely stopped. The French Regulations Authorities have been informed. To date, no contact from the media.
Potential Outcome
Environmental and health nuisances; damage to BP image .
What Went Wrong (Critical Factors)
- Lack of judgment : The control room operator increased the contents of one reactor which led to the process upset.
- No use of fire water gyromonitors which would have decreased partially the consequences of the vent via condensation of the vapors .
- Inadequate safety devices No means to catch or condense the vapors during an emergency reactor vent .
- Equipment - Other: The contents of the reactors were fairly high and possibly outside the operating window.
- Inadequate Recall of Training Material: There was no evidence that the operator was aware of the consequences of increasing the contents of the reactor .
- Inadequate correction of prior incident: a similar incident occurred in June 2001 .No adequate corrective action was taken.
- Inadequate technical design: The design input was obsolete.
- Procedures: - This critical factor refers to the operating window of the process. Potential situation not covered: the emergency procedure does not call for fire water use in case of venting .
What Went Well
1· The duration of venting was properly managed and reduced to the minimum
2· The plant fire brigade was responding well
3· Good internal and external communication
Lessons Learned
- Operators should be remembered / trained regarding the hazards of running the process close to the operating window.
- Although venting of the reactor is part of the emergency procedure, the potential consequences were not sufficiently assessed. Adequate safety devices will be provided .
Key Messages
Emergency VOC vent to the atmosphere is no longer tolerated .Risk assessment should be conducted to avoid the consequences of such incidents
Location Of Incident : Wingles, france
Date Of Incident : 28th, April 2006
Brief Account Of Incident
the reactor was vented for 10 minutes while full cooling At 8h00 pm , April 28, 2005 , an operational problem due to too a high polymer melt viscosity led to a an emergency shut-down of crystal line n° 2 in Wingles site. As per the emergency procedure, rarely used, was applied . The estimated vapor release is 1.3 t . Under weak windy conditions, styrene odors were detected by neighborhood community. Fire brigade has been called for enquiry. The odor disappeared within 30 minutes and the operations were successfully and safely stopped. The French Regulations Authorities have been informed. To date, no contact from the media.
Potential Outcome
Environmental and health nuisances; damage to BP image .
What Went Wrong (Critical Factors)
- Lack of judgment : The control room operator increased the contents of one reactor which led to the process upset.
- No use of fire water gyromonitors which would have decreased partially the consequences of the vent via condensation of the vapors .
- Inadequate safety devices No means to catch or condense the vapors during an emergency reactor vent .
- Equipment - Other: The contents of the reactors were fairly high and possibly outside the operating window.
- Inadequate Recall of Training Material: There was no evidence that the operator was aware of the consequences of increasing the contents of the reactor .
- Inadequate correction of prior incident: a similar incident occurred in June 2001 .No adequate corrective action was taken.
- Inadequate technical design: The design input was obsolete.
- Procedures: - This critical factor refers to the operating window of the process. Potential situation not covered: the emergency procedure does not call for fire water use in case of venting .
What Went Well
1· The duration of venting was properly managed and reduced to the minimum
2· The plant fire brigade was responding well
3· Good internal and external communication
Lessons Learned
- Operators should be remembered / trained regarding the hazards of running the process close to the operating window.
- Although venting of the reactor is part of the emergency procedure, the potential consequences were not sufficiently assessed. Adequate safety devices will be provided .
Key Messages
Emergency VOC vent to the atmosphere is no longer tolerated .Risk assessment should be conducted to avoid the consequences of such incidents
06 June 2006
Fire Hose Failure
Safety Incident Topic : Fire Hose Failure
Location Of Incident : Polyethylene Malaysia
Date Of Incident : 24th February 2003
Brief Account Of Incident
At approximately 23:45hrs on Sunday 24th February 2003 PEMSB Operation ‘A’ shift started their monthly fire drill. The drill was basically a practice of handling a fire hose. They completed setting up the hoses to the breach and hydrant then started to line up the firewater. After about 5 minutes the Team Leader realized that the water pressure was not very high. He therefore proceeded to the hydrant to increase the opening of the firewater valve. On his way back towards the breach the 2½” hose started snaking for about 10 secs before it separated from the coupling. The hose swung around a radius of approx 10ft for about 15 secs before the firewater isolated by the Team Leader. He was about 5 to 6 meters away from the breach when the hose burst. Upon checking it was found that only the hose was separated while the coupling was still intact to the breach. The binding of the hose was found 10 meters away from the breach. The drill was immediately stopped.
Potential Outcome
Injury to personnel from flying hose or binding
Critical Factors
· Failure of the fire water hose binding
· No checking of the condition of the firewater hose prior to use.
Location Of Incident : Polyethylene Malaysia
Date Of Incident : 24th February 2003
Brief Account Of Incident
At approximately 23:45hrs on Sunday 24th February 2003 PEMSB Operation ‘A’ shift started their monthly fire drill. The drill was basically a practice of handling a fire hose. They completed setting up the hoses to the breach and hydrant then started to line up the firewater. After about 5 minutes the Team Leader realized that the water pressure was not very high. He therefore proceeded to the hydrant to increase the opening of the firewater valve. On his way back towards the breach the 2½” hose started snaking for about 10 secs before it separated from the coupling. The hose swung around a radius of approx 10ft for about 15 secs before the firewater isolated by the Team Leader. He was about 5 to 6 meters away from the breach when the hose burst. Upon checking it was found that only the hose was separated while the coupling was still intact to the breach. The binding of the hose was found 10 meters away from the breach. The drill was immediately stopped.
Potential Outcome
Injury to personnel from flying hose or binding
Critical Factors
· Failure of the fire water hose binding
· No checking of the condition of the firewater hose prior to use.
02 June 2006
High Potential To Death
Safety Incident Topic: High Potential To Death
Location Of Incident: Geel, Belgium
Date Of Incident: 10th, April 2002
Brief Account Of Incident
· Cover plate of the electrical connecting box was removed to enable motor removal from equipment.
· Removal of cover plate created sharp edge that made contact with the lifting strap.
· During reinstallation, the workers experienced problems to position the motor and had to manoeuvre it to enable reconnection.
· The lifting strap was cut over sharp edge of the connecting box.
· The motor fell down on the leg of one of the workers.A second worker jumped away and experienced a slight cut.
· The lifting chain caught the motor and kept it hanging in the air and prevented the motor from falling on the next platform 2 m down.
What Went Wrong
· The lifting works were not stopped to evaluate the situation at the moment the job was perceived to be more complex than initially anticipated.
· The sharp edge was not noticed (was covered with plastic bag) and so the risk was not seen.
· A lifting strap was used that was overdue on approval.
What Went Well
· Medical treatment and follow-up.
· Quick response from mechanics involved to safely position motor.
Lessons Learned
1· Lifting training is needed that covers how to deal with sharp edges.
2· Evaluate who should be trained to do (manual) lifting works.
3· Improve warehouse storage process to have sufficient approved safety material available.
4· Evaluate what ideas can be copied from TAR’s during a smaller stop (eg container with safety material in unit).
5· Evaluate need for a plant-wide procedure/checklist for doing (manual) lifting works.
6· Evaluate what ideas can be copied from TAR’s during a smaller stop (eg container with safety material in unit).
7· Evaluate need for a plant-wide procedure/checklist for doing (manual) lifting works.
Location Of Incident: Geel, Belgium
Date Of Incident: 10th, April 2002
Brief Account Of Incident
· Cover plate of the electrical connecting box was removed to enable motor removal from equipment.
· Removal of cover plate created sharp edge that made contact with the lifting strap.
· During reinstallation, the workers experienced problems to position the motor and had to manoeuvre it to enable reconnection.
· The lifting strap was cut over sharp edge of the connecting box.
· The motor fell down on the leg of one of the workers.A second worker jumped away and experienced a slight cut.
· The lifting chain caught the motor and kept it hanging in the air and prevented the motor from falling on the next platform 2 m down.
What Went Wrong
· The lifting works were not stopped to evaluate the situation at the moment the job was perceived to be more complex than initially anticipated.
· The sharp edge was not noticed (was covered with plastic bag) and so the risk was not seen.
· A lifting strap was used that was overdue on approval.
What Went Well
· Medical treatment and follow-up.
· Quick response from mechanics involved to safely position motor.
Lessons Learned
1· Lifting training is needed that covers how to deal with sharp edges.
2· Evaluate who should be trained to do (manual) lifting works.
3· Improve warehouse storage process to have sufficient approved safety material available.
4· Evaluate what ideas can be copied from TAR’s during a smaller stop (eg container with safety material in unit).
5· Evaluate need for a plant-wide procedure/checklist for doing (manual) lifting works.
6· Evaluate what ideas can be copied from TAR’s during a smaller stop (eg container with safety material in unit).
7· Evaluate need for a plant-wide procedure/checklist for doing (manual) lifting works.
Oil Tank Fire Explosion
Safety Incident Topic: Fire Explosion In Thai Oil
Location Of Incident: Thai Oil
Date Of Incident: Not Known
Brief Account Of Incident
One of the gasoline tanks was overflowed. A security guard detected a strong smell and notified shift control who sent two operators to investigate. They don’t walk but they drive. Say no more, the bang was so big and shock the apartment building in Pattaya about 20kms away.
The fire spread from one tank to 4 others before it was contained and eventually put out by allowing the fuel to completely burn out, over 100,000 litres. There was 8 fatalities and 13 hospitalized with serious injuries. Fortunately it had occurred during silence hours and save over 100 people as admin building, maintenance workshop store and medical center were either completely gutted or severely damaged by the blast.


Location Of Incident: Thai Oil
Date Of Incident: Not Known
Brief Account Of Incident
One of the gasoline tanks was overflowed. A security guard detected a strong smell and notified shift control who sent two operators to investigate. They don’t walk but they drive. Say no more, the bang was so big and shock the apartment building in Pattaya about 20kms away.
The fire spread from one tank to 4 others before it was contained and eventually put out by allowing the fuel to completely burn out, over 100,000 litres. There was 8 fatalities and 13 hospitalized with serious injuries. Fortunately it had occurred during silence hours and save over 100 people as admin building, maintenance workshop store and medical center were either completely gutted or severely damaged by the blast.


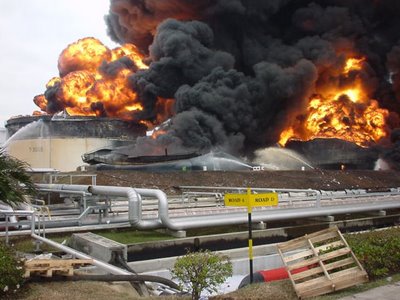
Subscribe to:
Posts (Atom)